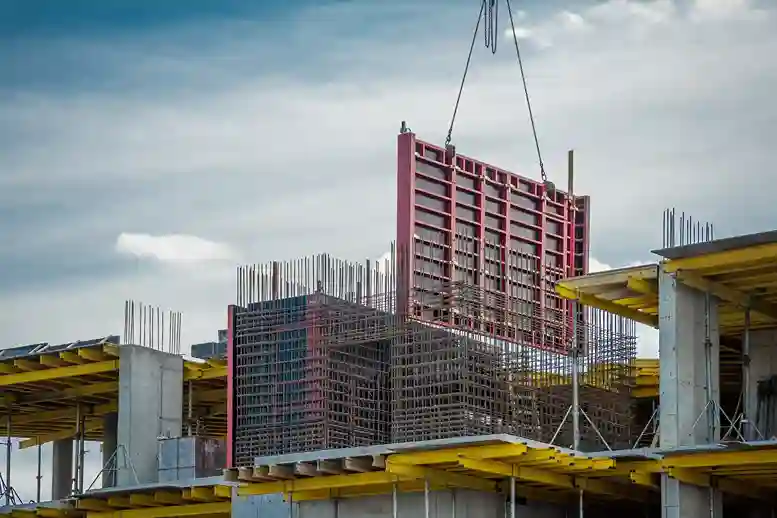
In the fast-moving world of construction and property development, the decisions made in the early stages can either streamline the entire process—or stall it. One of the most fundamental decisions on any concrete structure is the choice of formwork. It’s not just a construction detail; it’s a strategic move. Whether you’re a developer overseeing a visionary high-rise or a contractor navigating tight timelines, choosing the right formwork system—traditional, modular, or hybrid—can mean the difference between smooth execution and costly delays.
This guide aims to help developers, contractors, civil, industry partners, and clients better understand how to match the right formwork approach to your project’s unique scope and ambition. We’ll also explore how our team at Future Form is redefining modular formwork to help our clients reduce labour costs, cut down construction time, and future-proof their project gains.
Understanding Your Options: Traditional, Modular and Hybrid Formwork
Let’s break down the three primary systems:
1. Traditional Formwork
Traditional formwork is the oldest and most widely recognised system, often built from timber, plywood, or steel. It offers a high degree of flexibility and is usually crafted onsite to fit custom designs.
Pros:
- Great for intricate or non-standard shapes
- Easy material sourcing
- Familiarity across most construction teams
Cons:
- Labour-intensive
- Time-consuming setup and stripping
- Prone to human error and material waste
For small-scale or highly customised builds, traditional formwork can still be a solid choice. However, on larger commercial or repetitive builds, its limitations quickly surface.
2. Modular Formwork
Modular formwork uses pre-engineered panels and systems—like the ones we develop at Future Form—to create efficient, reusable setups. Built offsite, transported easily, and installed quickly, modular systems are growing in popularity across Australia.
Pros:
- Faster installation and stripping
- Reduced on-site labour and safety risks
- Reusable across multiple projects
- Precise and consistent outcomes
Cons:
- Higher upfront costs
- May be less flexible for complex designs
This system is ideal for high-volume, repetitive projects—think multi-residential developments, infrastructure projects, or commercial sites with consistent geometry.
3. Hybrid Formwork
A hybrid system combines elements of both traditional and modular approaches. It offers a tailored solution where pre-engineered panels form the core of the build, and traditional methods are used to manage architectural complexities.
Pros:
- Best of both worlds: efficiency and adaptability
- Great for transitioning project scopes
- Can support sustainability and waste reduction goals
Cons:
- Requires careful planning and integration
- Not all teams are experienced in hybrid use
Hybrid systems are becoming especially useful on projects that evolve over time or where sections of a building vary in complexity.
Choosing the Right System for Your Project Scope
So how do you choose?
At Future Form, our team works with developers and contractors from Sydney to Canberra, and we’ve seen firsthand that there’s no one-size-fits-all answer. The best formwork system depends on five main considerations:
1. Project Scale and Repetition
- Large-scale developments with repetitive elements (e.g. apartment blocks or commercial towers) are ideal for modular or hybrid solutions.
- Smaller, boutique developments with one-off architectural features may benefit from traditional formwork.
2. Project Timelines
- Shorter timelines demand faster installation and stripping. Modular systems are clear winners here.
- If you’re on a relaxed schedule and your team is comfortable with traditional techniques, traditional formwork can suffice.
3. Labour Availability
- Labour shortages in Australia are pushing more contractors towards modular systems.
- At Future Form, our modular systems are engineered to be assembled with minimal on-site labour, supporting projects facing skill shortages.
4. Design Complexity
- Intricate shapes and curves are more suited to traditional methods—or hybrid systems where Future Form panels can form the majority of the structure, with custom work built around them.
- Simpler layouts benefit from repeatable, modular designs.
5. Budget Constraints
- While modular formwork comes with higher upfront costs, it leads to long-term savings through reuse, reduced labour, and faster cycles.
- Traditional systems may appear cheaper initially but can increase costs through inefficiencies and rework.
Why More Developers Are Choosing Modular in 2025
Across many countries, there’s a strong trend towards smarter, scalable construction practices. With rising material costs, increased demand for housing, and sustainability pressures, developers are re-evaluating traditional methods.
Future Form’s modular formwork systems align perfectly with these demands. Here’s why:
Labour Cost Reduction
We’ve designed our systems to be intuitive and easy to use, reducing the need for large on-site teams. In many of our recent Sydney-based high-rise projects, clients cut down their labour costs by up to 30%.
Faster Turnaround
Our clients regularly report shorter construction timelines—some by as much as 25%—thanks to the streamlined assembly and disassembly of our panels. Less downtime means more profit and fewer hold-ups.
Improved Site Safety
Less manual handling and more predictable assembly reduce on-site incidents. Our formwork systems are engineered with safety and compliance at the forefront.
Reusability and Sustainability
A single Future Form system can be reused across multiple sites, reducing construction waste and environmental impact—something more clients are now considering under Australia’s Green Star and NABERS ratings.
Case in Point: A Hybrid Success at the Australian War Memorial
One of Future Form’s most notable hybrid formwork achievements was at the iconic Australian War Memorial redevelopment in Canberra. As a nationally significant site, the project demanded precision, care, and adaptability to navigate heritage elements while delivering on a modern extension to support growing visitor numbers.
Our solution? A hybrid system:
- Modular Future Form panels were used extensively for new structural elements to maximise efficiency and consistency
- Traditional formwork was applied to heritage-sensitive zones requiring bespoke shaping and non-invasive installation
The result:
- Major time savings during the build phases, ensuring alignment with tight government schedules
- Labour demand significantly reduced without compromising craftsmanship
- Seamless integration between old and new structures, respecting the site’s legacy while equipping it for future generations
Modular, But Make It Future Form
When developers and contractors hear “modular formwork,” they often think of generic systems that work well enough. But we believe modular should mean more than efficiency—it should mean performance, adaptability, and a genuine uplift to your entire construction process. That’s why at Future Form, we approach modular differently: not just as a product, but as a complete, collaborative solution tailored to your project’s needs.
Not all modular systems are equal. At Future Form, our team pride ourselves on the engineering detail, quality control, and local support that sets us apart:
- Australian-designed and fabricated: Our systems are purpose-built for Australian conditions and codes.
- Customisable modular kits: We work with developers to create tailored modular solutions, not just off-the-shelf panels.
- On-site training and support: Our engineers provide full training and ongoing site visits to ensure your team is confident from day one.
We don’t just drop off materials—we partner with you for the long haul.
Final Thoughts: Investing in Long-Term Performance
Choosing the right formwork system is more than a short-term cost decision—it’s a long-term investment in your project’s success. As the industry moves towards smarter, more sustainable solutions, modular and hybrid formwork systems are proving their value not just in savings, but in safety, speed, and scalability.
At Future Form, we’re committed to helping developers and contractors make informed choices that lead to better builds. Whether you’re planning your next apartment complex in Melbourne or a civic centre in Newcastle, our team is here to help you build smarter from the ground up. Need help assessing which formwork approach is best for your next project? Let’s work it out together.
References
Australian Bureau of Statistics. (2023). Labour Force, Australia, Detailed. https://www.abs.gov.au/statistics/labour/employment-and-unemployment/labour-force-australia-detailed
Green Building Council of Australia. (2024). Green Star – Design & As Built. https://new.gbca.org.au/
Standards Australia. (2023). AS 3610: Formwork for Concrete. https://www.standards.org.au/
Safe Work Australia. (2023). Construction Industry Profile. https://www.safeworkaustralia.gov.au
Future Form. (2025). Projects and Services Overview. https://futureform.com.au/