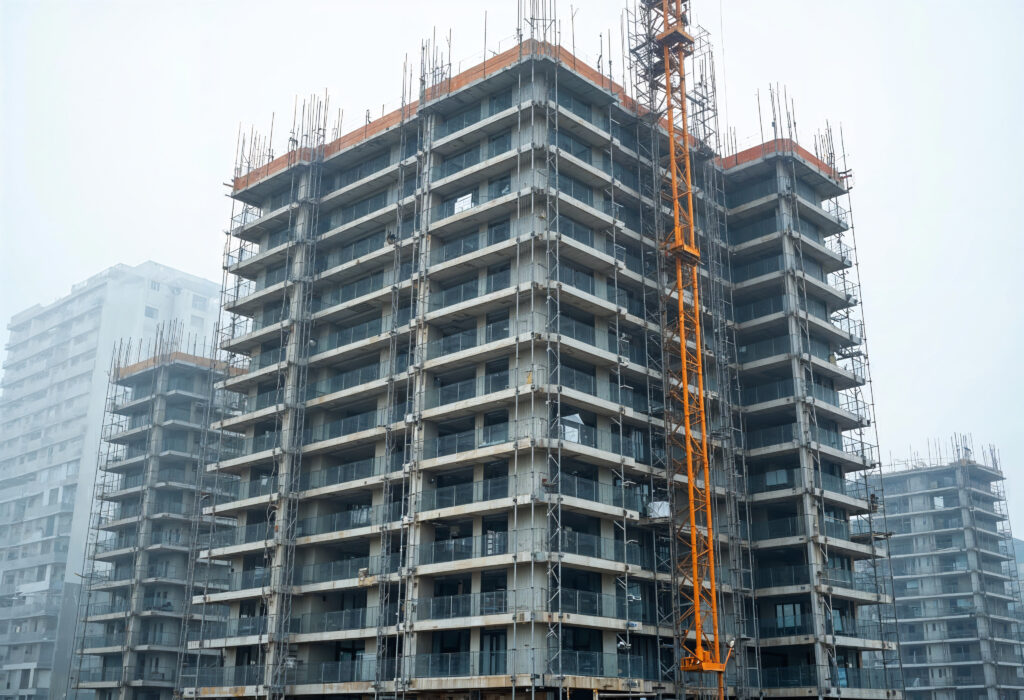
High-rise construction is racing to meet the needs of urban expansion, together with labour shortages and increasingly tightening demands for faster, safer, and more sustainable construction sites. It is no longer just how high we can go — it’s about how smart we build while going up.
Across skylines, a quiet revolution is underway. The combination of prefabricated concrete and traditional formwork is transforming the landscape for developers, builders and property investors. It’s a hybrid solution, faster, sharper, and more precise — and Future Form is at the forefront of making it happen.
This isn’t about choosing between old and new. It’s about using both, together, to reimagine what’s possible.
The Construction Shift: Why Hybrid Matters Now
The construction industry has always been a leader in innovation, but in the past few years this sector has faced new obstacles. A lack of labor, cost pressures, supply chain shortages and stricter environmental goals are forcing the industry to change — fast.
And pre-fabrication, especially in concrete, has been a crucial aspect of that response. It is quick to make, reliable and sustainable. But on complicated sites — or particularly in high-rise buildings — pre-fabrication is not the answer for every detail. That’s where formwork really shines.
Rather than relying on one or the other, leading projects are embracing both. When prefab concrete encounters custom-designed formwork, the advantages are clear: durations shorten, quality assurance strengthens, and site operations streamline.
What Is Hybrid Concrete Construction?
Hybrid construction is, fundamentally, about mixing and matching prefab concrete components — like walls, stairs, or façade panels — with conventional in-situ pours made possible by various formwork systems. It’s a best-of-both-worlds approach:
- Prefabricated elements are manufactured offsite in highly controlled environments. This ensures uniformity, reduces waste, and slashes onsite labour time.
- Formwork construction allows for flexibility, adaptability, and detailed structural elements to be poured exactly where and when needed.
Combined, these two techniques grant builders the versatility of traditional methods and the speed of modern manufacturing — all necessary on high-rise sites where time is money.
The Key Advantages of the Concrete + Formwork Combination
This hybrid method is gaining traction across the world because it solves several real-world problems for construction teams, developers, and clients:
Accelerated Timelines
Offsite precast production can occur while site work or lower-floor formwork pours are in progress. This parallel process takes weeks — sometimes months — off a project timeline.
Improved Safety
Fewer trades working at heights and less onsite material handling contribute to a safer site environment — something that remains a priority for the construction industry.
Greater Precision
Company-made parts mean tighter control over quality and less re-work. Used in conjunction with good quality formwork, tolerances are tighter, joints are neater and finishes are more consistent.
Environmental Efficiency
Hybrid construction leads to less onsite waste and fewer transport trips. It also supports green building standards, helping developers meet sustainability benchmarks.
Adaptability for Complex Designs
Certain structural features — like curved facades or irregular cores — are often more efficiently handled with formwork. Meanwhile, repetitive elements like bathroom pods or floor panels are ideal for prefabrication.
Collaboration Is Key
Coordination is the key to successful hybrid construction. Developers, engineers, builders, and suppliers should be in sync right from the start. Questions like these need to be addressed early:
- Which components should be prefabricated?
- Which ones require in-situ pours?
- What’s the most efficient sequence for each stage of the build?
That’s where Future Form brings its edge.
Suppliers and Industry Partners: Working Together for Smarter Builds
This approach thrives on partnerships — and supplier networks play a massive role. From high-performance concrete mixes to advanced crane scheduling, every moving part matters.
Future Form regularly collaborates with local engineering teams, scaffolders, crane operators, and transport providers to ensure that our prefabricated elements and onsite formwork are perfectly synchronised. Our teams are proud to work with forward-thinking suppliers who understand the balance between control and customisation.
If you’re a supplier, subcontractor, or partner interested in pushing the boundaries of construction innovation, we’d love to talk.
Future Form’s Approach: The Hybrid Model in Action
At Future Form, we don’t just deliver concrete and formwork. We deliver tailored strategies that respond to the specific needs of each project — right from the concept stage.
Our team collaborates closely with architects, engineers, developers and site managers to find the right balance between concrete and formwork methods. It’s always about trying to simplify and streamline where possible whilst maintaining structural performance and architectural aesthetic.
A standout example of this in practice is the King & Phillip Residences in Sydney’s CBD. Situated among heritage landmarks and bustling pedestrian routes, this high-rise build posed several logistical and architectural challenges. Time, space, and precision were all under pressure.
Future Form came in with a hybrid strategy. We’ve employed off-site precision-manufactured precast façade panels to streamline the exterior structure. Twinwall and system designed proprietary formwork was employed for the vertical cores and in-situ concrete slabs were cast on site.
The outcome? The build was considerably quicker than a traditional process, required significantly fewer cranes and delivered an intricate design with minimal disruption to surrounding heritage.
This approach isn’t a one-off. It’s the foundation of how we operate — combining thoughtful prefab integration with adaptable formwork solutions across most ambitious builds.
Looking Ahead: The Smarter, Greener Future of High-Rise Construction
In a landscape where every hour counts and every detail matters, the union between prefabricated concrete and custom formwork is rewriting all the rules. It’s faster. It’s smarter. And when done right, it elevates not just the building — but the entire build process.
At Future Form, we’ve spent years refining the art of hybrid construction. We understand the pressures you face — from tight timelines to challenging designs — and we offer solutions that transform vision into vertical reality.
So whether you’re breaking ground on your next project or will simply never settle for “good enough,” we’re here to help you build better.
References
Australian Bureau of Statistics. (2023). Construction Work Done, Australia, Preliminary. https://www.abs.gov.au/statistics/industry/building-and-construction
Engineers Australia. (2022). State of the Engineering Profession Report. https://www.engineersaustralia.org.au
PrefabAUS. (2023). Innovation in Prefabrication: Annual Report. https://www.prefabaus.org.au
Safe Work Australia. (2023). Construction Industry Profile. https://www.safeworkaustralia.gov.au
Standards Australia. (2022). AS 3850: Prefabricated Concrete Elements. https://www.standards.org.au/