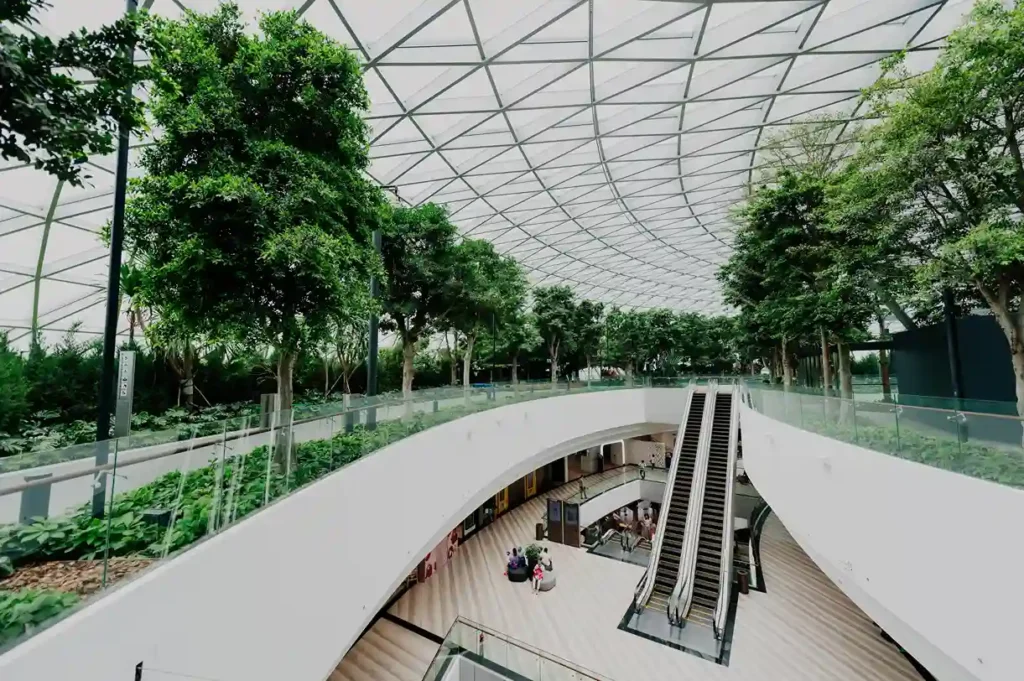
On the ever-changing property development, achieving the right balance between speed, quality, and design flexibility has long been a challenge. But what if developers could check all the boxes — with no compromises? That may be closer than we think thanks to advances in modular construction. It’s today’s reality.
Future Form is proud to be leading this transformation. As specialists in modular and prefabricated building solutions, we’re enabling developers, architects, and clients to pursue visionary projects that are both efficient and beautifully bespoke. In this blog, we explore how customisation and efficiency no longer sit at opposite ends of the scale, and why modular design is at the heart of construction’s future.
What Is Modular Design, Really?
Let’s start with the basics. In modular construction, building elements, or modules, are built off-site in a factory setting. These units are then moved and connected on-site, forming a whole building. It’s a process that nearly eliminates downtime on timelines, minimizes site disruption, and increases accuracy.
Unlike older prefab models, today’s modular buildings are anything but generic. Thanks to advanced design tools and smarter manufacturing techniques, modules can be customized to meet specific site conditions, architectural visions, and end-user needs—all without stalling the works.
Breaking the Myth: Prefab Doesn’t Mean Basic
There’s a lingering misconception that prefab means plain or repetitive. In reality, modular systems now offer significant architectural freedom. The modular approach by Future Form makes it possible to customize layouts, be creative with structural design, and to consider site specific solutions. From sinuous balconies to cantlevered walkways, we’re pushing the limits.
Need a high-rise that doesn’t have the scale but sits flush in a heritage site. Done. How about a 2-3 level commercial build with variable heights and varied facade treatments? Easy. With our expertise and technology, modular construction is delivering premium results, fast.
Efficiency Without Compromise
While the aesthetic flexibility of modular construction is a major drawcard, its efficiency is what seals the deal. Prefabricated projects can be completed from 30-50% faster than others, which is a huge benefit for such high-demand industries as education, healthcare and residential sectors.
By manufacturing modules off-site, we eliminate weather delays and on-site congestion. This significantly lowers holding costs and shortens the time between concept and completion. In fast-growing suburbs or remote regions, these time savings are critical.
Quality control is also a huge plus. Our modules are built in controlled environments with CNC machines, digital modeling, and inspections. In other words, consistent, high-quality results that you can trust to meet or exceed industry standards — every time.
Modular construction also enhances safety. Construction is one of the most dangerous industries, with the levels of risk manageable. We can do this by removing a lot of the construction process off-site, lessening onsite exposure and risk of accident.
Technology Drives Innovation
None of this would be possible without cutting-edge technology. Modular design is fuelled by digital tools that improve accuracy, speed, and coordination across every stage.
We rely heavily on Building Information Modelling (BIM), which allows stakeholders to visualise and refine the project before physical work begins. BIM is the tool that prevents design conflicts, and enables early decision making—both things which save time and costs.
Precision is driven by CNC (Computer Numerical Control) machines, which pre-cut materials to very precise measurements. Together with the help of AI-optimized scheduling tools, our production goes like clockwork, which means predictable, on-time delivery.
These two tools help us perform complicated customisation without sacrificing modularity.
Looking Ahead: Investing in the Future of Modular
Modular construction has proved itself — but innovation never stops. With demand surging for smarter, greener buildings — from both a design and a construction standpoint — the question that remains is less about whether modular can deliver, and more about how far it can go. For us the solution rests in a relentless focus in three specific areas: sustainability, design flexibility, and collaboration.
At Future Form, we’re not content with the status quo. We’re committed to pushing modular design to new limits—building faster, building smarter, and building with intention. Whether it’s a luxury high-rise in the CBD, a public education facility in Sydney, or a heritage-sensitive civic upgrade, we believe modularity is the key to unlocking high-performance builds at scale, without sacrificing individuality or responsibility.
R&D of New Sustainable Materials
We are making significant investments in low-carbon and carbon-negative materials, for instance developing advanced wall systems, recycled content composites and bio-based substitutes. These materials don’t just minimise a building’s environmental impact — they improve performance and durability in various climates. We want to incorporate sustainability throughout the structures, not only in the finishes.
Flexible Module Design Systems
Forget the idea that modular means monotonous. Our design teams are creating systems that allow for sweeping curves, hybrid forms, and complex architectural features—all while preserving the core efficiency of modular workflows. From multi-use urban spaces to premium towers with dynamic façades, we’re enabling architects and developers to dream big without delaying timelines.
Greater Community and Industry Engagement
Our team bridging the gap between innovation and adoption through open collaboration. We work closely with councils, developers and the wider industry to influence policy and attitudes around modular building. Via site visits, stakeholder sessions and educational partnerships, we are raising awareness about what is possible, today — and educating the next generation to take modularization even further.
Customisation in Action: Future Form Projects
Customisation is not just a buzz word for us at Future Form—it is inherent to all projects our team delivers. Consider our work on the Australian War Memorial in Canberra. Heritage replica materials had to meet exacting standards at this highly Sensitive site using state of the art hybrid formwork. Our suite of modules for the ANZAC Hall and glazed link kept disruption to a minimum, while boosting build speed.
We also delivered highly tailored solutions at The Establishment, a luxury residential complex in Sydney. From receptionist to sculpted spa zones, we developed custom formwork that enabled the vision of resort-style living to come to life on a strict timeline.
And then there’s 88 Walker Street in North Sydney. This soaring mixed-use tower posed complex design challenges—from hotel-level finishes to commercial-grade efficiency. Our high-performance modular systems enabled diverse internal fit-outs without sacrificing build speed or quality.
Final Thoughts: Vision Meets Practicality
The modular design is officially out of the box. It has since developed into one of the most flexible and versatile options for developers, construction companies, and clients worldwide. And at Future Form, we consider it more than a trend — it’s a construction revolution.
What we tell industry partners, suppliers or more forward-thinking developers is: “You don’t have to compromise. With the right team and the right systems, customisation and efficiency can co-exist side by side. When it’s done right, modular construction does both.
References
McKinsey & Company. (2019). Modular construction: From projects to products. Retrieved from https://www.mckinsey.com
Safe Work Australia. (2023). Work-related injuries statistics. Retrieved from https://www.safeworkaustralia.gov.au/statistics-and-research
University of Melbourne. (2022). Sustainability benefits of modular construction in Australia. Faculty of Architecture, Building and Planning.
Future Form. (2024). Projects. Retrieved from https://futureform.com.au/projects/